Additive Manufacturing and Upcoming Advances
Session by Dr. Dwarak Krishnan as part of Webinar Series “To Guide Engineering Students to select meaningful projects”
Additive manufacturing (AM) is rapidly evolving while increasing in scalability and strategic possibilities. Manufacturing leaders across most industries are adopting additive manufacturing across their enterprise and benefiting from the flexibility that this technology brings to their value chain.
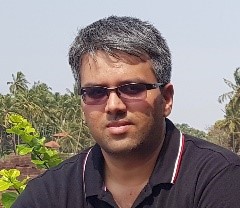
Dr. Dwarak KRISHNAN, Industry Process Consultant Manager, Dassault Systemes with his 15 years of experience explains us about Additive manufacturing and transformation in manufacturing trends this technology has ushered in.
Advancement in Additive Manufacturing, Simulation played key role in transformation in conventional manufacturing, which is predominantly a subtractive manufacturing. Additive manufacturing allows us to design parts of intricate shapes, whereby, we can reduce material and weight of the part, which gives us advantage of cost reduction.
Additive manufacturing technology has been increasingly important & relevant to the next generation of advanced manufacturing. Previously associated with hobbyists using conventional PLA & ABS material, additive manufacturing is now widely accepted and recognized as the next generation of manufacturing. With improving technologies reducing the production cost, 3D printing is revolutionizing its way across various industries – from manufacturing to healthcare, energy, defence and aviation.
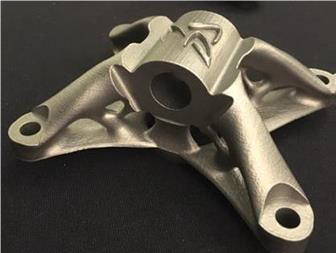
In addition, Additive Manufacturing comes with lots of benefits, as restriction to manufacturing with this technique are very less. We can manufacture designs inspired by nature, which helps us to optimize the design in terms of material, process and at the same time provides same strength. It also helps to reduce cost of manufacturing almost to the tune of 50% in some of the components. Particularly in Aerospace industry, any reduction in weight, provides huge benefits and cost savings. Hence additive manufacturing is widely accepted by Aerospace Industry.
Additive manufacturing comes with lots of opportunities due to its one-step production method. With this feature, designer can design any complex shape for any industry without much constraints of manufacturing process. Additive manufacturing shows presence in almost every industry such as the automotive industry is implementing 3D printed parts like shift knobs and cylinder heads in both passenger and racing cars, lowering costs and improving performance. The aerospace industry is producing lightweight 3D-printed parts ranging from table trays to complex 3D-printed parts for jet engines to improve quality and save on energy consumption. The healthcare industry is using 3D printing technology to create medical items, such as prosthetics and organic material, to improve on custom designs for individual patients.
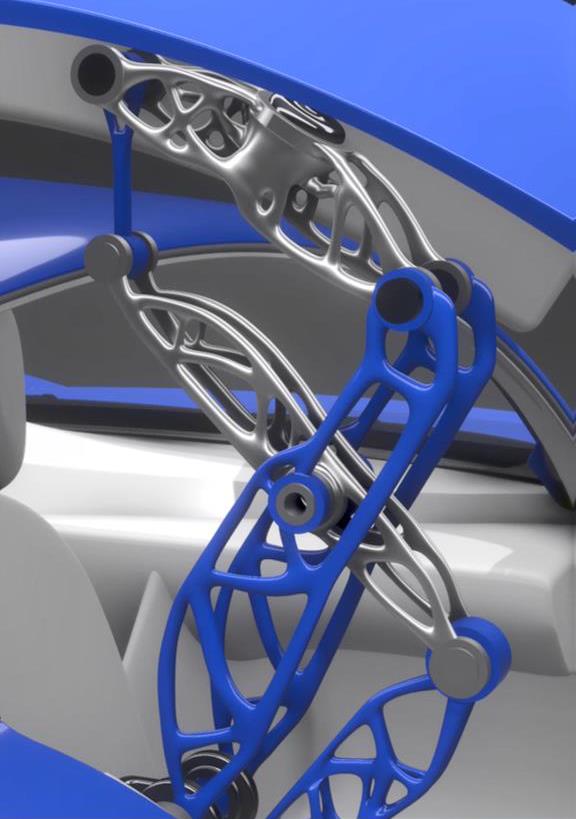
Advantages in Additive Manufacturing comes with certain challenges such as appropriate material selection in design, Scalability in manufacturing, constraints with respect to material for specific design, also durability of the product or consequences of potential failure of product. To resolve these challenges one need to design the product appropriately.
In order to explore power of Additive manufacturing, new technologies like Functional Generative Design helps us to leverage benefits of additive manufacturing process. Under this design process all members right from designer, manufacturing specialist to simulation engineer should work collaboratively in such a way that we can emphasize some of the key aspects of additive manufacturing such as cost, durability, Surface finish, weight, part properties and Support structure. Under this approach engineer can come up with organic design concept, which satisfies the constraints about weight, and provide same strength.
Now a days software are designed in such a way that you can virtually manufacture the part in software and generate machine code to manufacture real part in real additive manufacturing machine. With this Additive Manufacturing process planning technique, engineers can validate the process virtually for any kind of part to be manufactured.
Following are certain technologies, which are mainly used in Additive manufacturing –
- Powder Bed Fusion – This technology produce a solid part using a thermal source that induces fusion (sintering or melting) between the particles of a plastic or metal powder one layer at a time.
The limitations of PBF often center on surface roughness and internal porosity of the as-printed parts, shrinkage or distortion during processing and the challenges associated with powder handling and disposal. - Material Extrusion Method - Similar to how toothpaste is squeezed out of a tube, material extrusion technologies extrude a material through a nozzle and onto a build plate. The nozzle follows a predetermined path-building layer-by-layer. Material extrusion is a quick and cost-effective way of producing plastic prototypes. Industrial FDM systems can also produce functional prototypes from engineering materials. FDM has some dimensional accuracy limitations and is very anisotropic.
- Material Jetting - Material jetting is often compared to the 2D ink jetting process. Photopolymers, metals or wax that cure or harden when exposed to UV light or elevated temperatures can be used to build parts one layer at a time. The nature of the material jetting process allows for multi-material printing. This ability is often used to print support from different (soluble) material during the build phase.
Material jetting is ideal for realistic prototypes, providing excellent details, high accuracy, and smooth surface finish. The main drawbacks of material jetting technologies are the high cost and the brittle mechanical properties of the UV activated photopolymers. - Binder Jetting - Binder jetting is the process of dispensing a binding agent onto a powder bed to build a part one layer at a time. These layers bind to one another to form a solid component.
Ceramic-based Binder Jetting is ideally suited for applications involving aesthetics and form: architectural models, packaging, ergonomic verification etc. It is not suitable though for functional prototypes, as the parts are very brittle. - Direct Energy Deposition - Direct Energy Deposition (DED) creates parts by melting powder material as it is deposited. It is predominantly used with metal powders or wire and is often referred to as metal deposition. DED technologies are used exclusively in metal additive manufacturing. The nature of the process means they are ideally suited for repairing or adding material to existing components (such as turbine blades).
Such a detailed information about Additive Manufacturing and its application really helped students to explore new avenues and create new innovative projects in this area.
Thank you very much for conducting such wonderful session.