Industrial and Manufacturing Automation
Session by Mr. Prashanth MYSORE as part of Webinar Series “To Guide Engineering Students to select meaningful projects”
In the current competitive world, technology advancement and globalization has changed the nature of manufacturing. Development in areas like Robotics, Industrial Vision and Collaborative automation have opened up new capabilities in Manufacturing automation and many new opportunities for new age engineering.
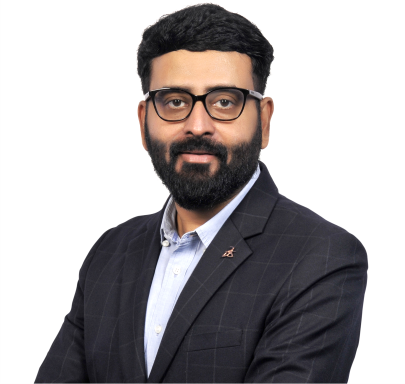
In this session, to enlighten engineering students, on industrial and manufacturing automation topic, we are interacting with Mr. Prashanth MYSORE, Senior Manager, Dassault Systemes. Prashanth is one of experts in the world of Innovation in manufacturing automation with 23 years of experience in this field. He won best IOT project Award in 2019.
While understanding this topic we first need to understand what is the need and impacts of Industrial Automation. Looking at current situation of pandemic, we already realized if automation was not in place, the world economy would have been in great danger. Thanks to Industrial automation, which keep this world economy running and alive. Our speaker Mr Prashanth Mysore highlighted that in post Covind-19 world, new employment opportunities will be generated in manufacturing sectors and it will generate great demand for skilled engineers.
To understand automation in detail, we need to explore how Industry has evolved in last century. We have progressed from Mechanized manufacturing to mass Production and from mass production to computerization of manufacturing processes. Now we are moving towards Cyber Physical Systems and IoT. This revolution in manufacturing asks for knowledge and skill development in different technologies such as Artificial Intelligence, IoT, and Additive Manufacturing, nanotechnology, Quantum computing, renewable energy and many more. Students need to be master in one of these technologies and should have at least primary knowledge of other technologies.
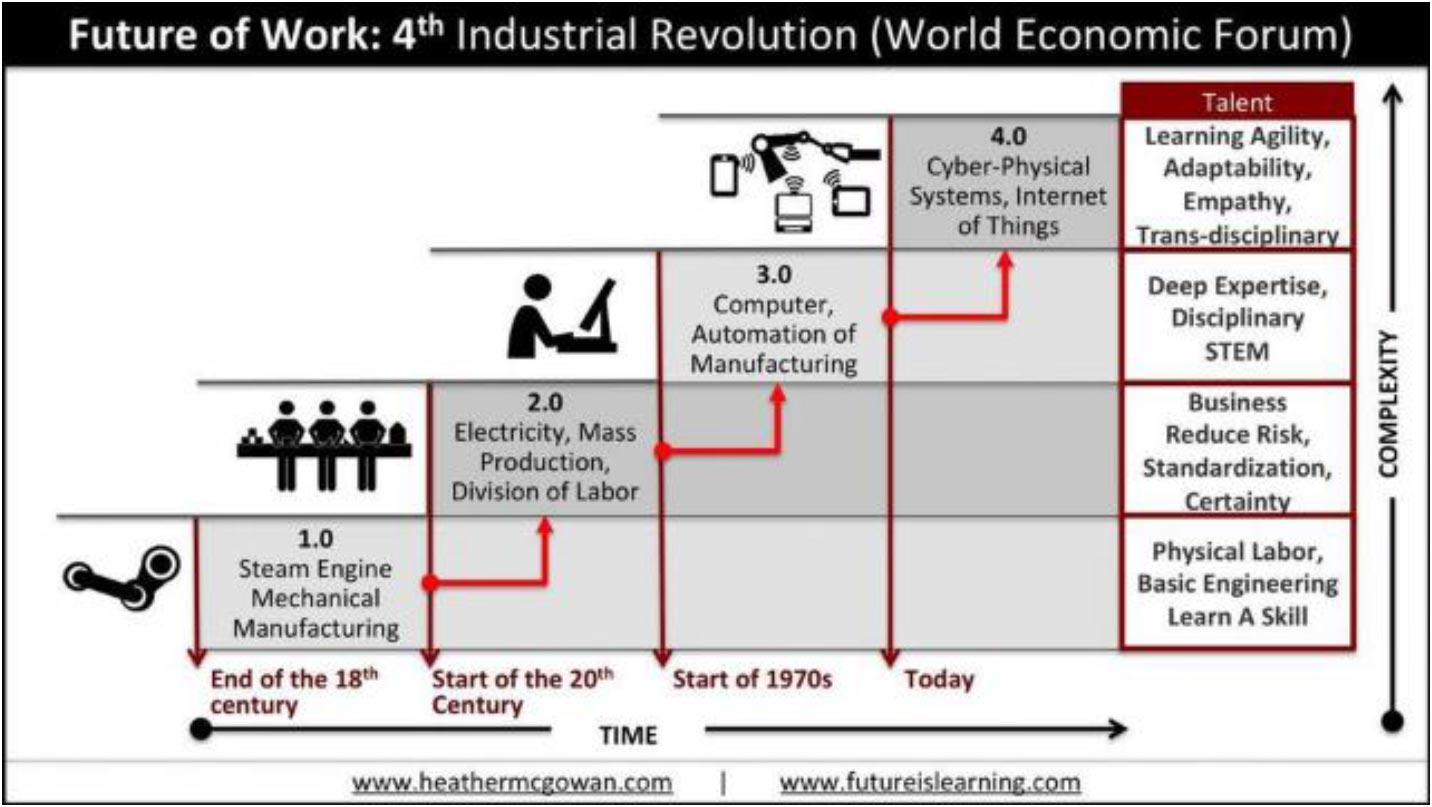
Industrial automation involves use of various control devices such as PLC, Sensors, DCS to control various operations of an industry without significant intervention from humans and to provide automatic control over performance. Industrial Automation involves usage of advanced control strategies like cascade controls, modern control hardware devices as PLC’s, sensors and other instruments for sensing the control variables, signal conditioning equipment’s to connect the signals to the control devices, drives and other significant final control devices, standalone computing systems, communication systems, alarming and HMI (Human Machine Interface) systems.
Industrial automation mainly helps us to achieve following objectives –
- Increase the productivity
- Reduce the production cost
- Improve product quality
- Increase flexibility in production
- Operator friendliness
- Improve safety
Based on the flexibility and level of integration in manufacturing processes, Automation Systems are classified into basic types –
- Fixed Automation – For high volume production, fixed automation system is useful. In Fixed Automation, sequence of operations to be performed are fixed. Examples of this automation system are automated assembly lines, discrete process, machine transfer lines.
- Programmable Automation - In this, sequence of operations can be changed by changing the program. Sequence of operations is varied based on the different product configurations. This type of system is used in batch processes, steel rolling mills, industrial robots, etc.
- Flexible Automation - It is the extension of the programmable automation. This offers a greater flexibility to deal with product design variations. Operators can give commands in the form of codes in the computer program if operator wants to change the sequence of the process. Most of the vehicle manufacturing uses such automation to manufacture different variants on the same production line without losing time in changeover.
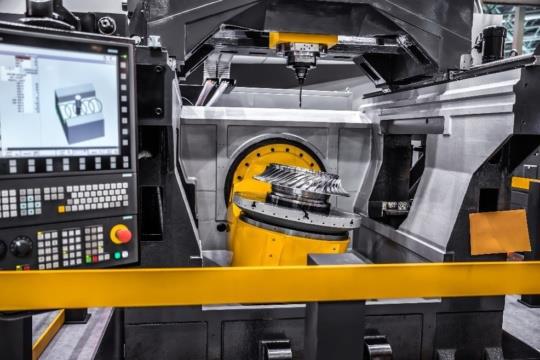
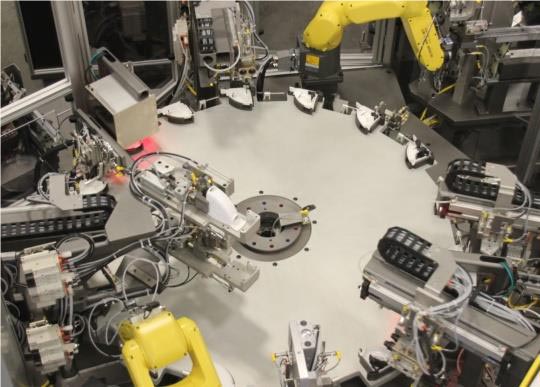
Robotics plays major role in digital manufacturing as it handles many jobs or work as assistants to human for carrying out laborious tasks. In robotic processing operations, the robot manipulates a tool to perform a process on the work part. Examples of such applications include spot welding, continuous arc welding, drilling, riveting and spray painting. Robots are useful for carrying out operations in very hazardous environment such as Nuclear Power plant. Now to make it more flexible and efficient, robotics is moving towards Collaborative Robots, called as COBOTS. It is capable of learning multiple tasks and helps human beings to carry out different tasks in industry.
Factory automation, or industrial automation, connected equipment helps in improving the efficiency and reliability of process control systems. This in turn leads to lower costs, improved quality, increased flexibility and less environmental impact.
Let us have a short tour of Automated Factory, which explains us how it improves profitability and efficiency of the production.
- Smart Supply Chain – By using simple GPS technology and proper tagging using RFID or BARCODE, Production engineer and Supply chain manager can track the material and provide exact information about production running time.
- Production in Collaboration – With the help of all data related with machine, raw material and proper process work instructions, production engineer can predict the throughput in advance and can provide correct estimation of production.
- Predictive Maintenance – With proper sensors and updated PLCs, maintenance engineer can predict in advance which machine will need maintenance and which type of maintenance it would need. This data in turn helps production engineer to plan his production as per the maintenance plan in advance. It avoids any abrupt disruption in the process for maintenance.
- Smart Manufacturing – In today’s age with the help of Virtual Twin of the manufacturing, manager can review operation from any remote location and it provides ability to troubleshoot from remote location if any mishap happens.
- Energy Optimization – In many developing countries, energy sources are very crucial and important factor, which impacts cost. According to manufacturing plan and raw material availability engineer can define a logic to run the machine or not. Eventually it will save energy and improves cost of production.
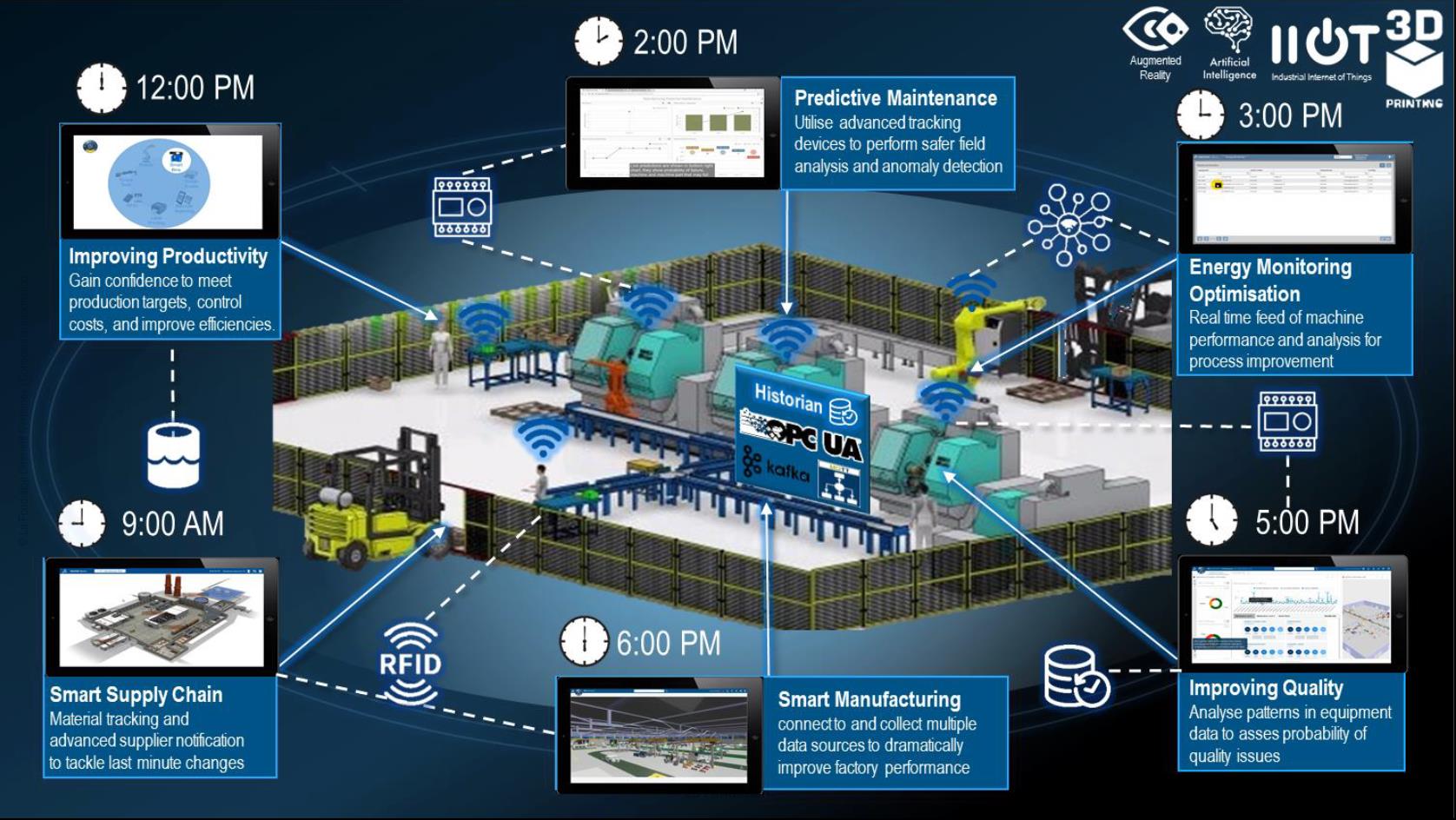
All these advanced technologies such as IIoT (Industrial Internet of Things), GPS, Industrial Sensors, Updated PLCs, Digital Twin, RFID, Barcode, Sensing mechanism, Big Data, Data Analytics helps to execute all processes in factory in automated way.
On a concluding note, Mr. Prashanth suggested students to be a master in one of these technologies and get knowledge for other connected technologies. He advised students to be a multi-disciplinary to address upcoming changes/advances in manufacturing domain.
Thank you very much Mr. Prashanth for all this insight into Manufacturing Automation and Robotics.
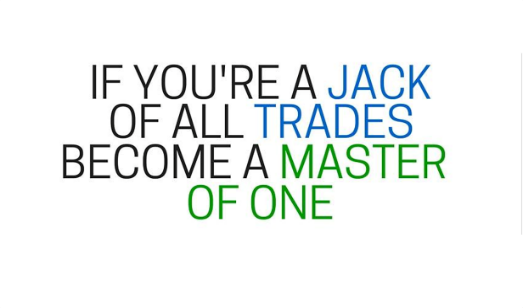